Cross-Laminated Timber (CLT) in the Construction of Nonresidential Buildings
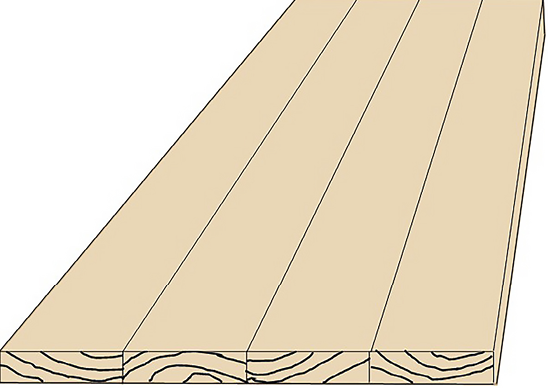
Wood has likely been used to build human structures throughout the existence of mankind. It is a renewable resource that is visually appealing. Over the past 60 years, foresters have substantially increased yields of southern yellow pines, providing an ample supply for the construction of nonresidential wood buildings. However, the inability to obtain extended-length pieces of wood that meet building codes has often limited the ability to use wood for the framing and structure of taller buildings.
There are other concerns about using wood in the construction of nonresidential buildings. For example, wood can be burned in fires and lose its structural capabilities. Fire-retardant wood can be used in residential construction to reduce ignition and minimize damage from fire. Many people do not realize that during intense fires in larger buildings, large structural pieces of wood will, in fact, hold their form better than steel, helping to maintain building integrity. Large pieces of wood only char and are not completely consumed in fires. Of course, this characteristic associated with larger pieces of wood (larger diameter trees of many species, for example) allows us to conduct prescribed burns in forests without substantial tree mortality.
Wood burns slowly and will char on the outside, sealing and protecting its interior. The build-up of carbon on the surface limits the oxygen supply to the interior wood and thus acts as an insulator. Remember the fire triangle: Heat, oxygen, and some source of fuel (in this case, wood) are needed for fire to continue. Steel is an excellent conductor of heat; during fires, the interior of a steel beam can get just as hot as the exterior. When metal reaches a critical temperature of 2,372 degrees Fahrenheit, it begins to melt and can catastrophically fail.
Even concrete can fail during fires, especially in the case of “explosive spalling.” When it is exposed to high temperatures, water in the concrete vaporizes quicker than it can escape, resulting in a rising vapor pressure that ultimately causes the concrete to explode. Such an event could cause catastrophic failure of structures.
Biodegradation of wood is another concern. With time, wood will decay and rot, losing its structural capabilities. Over the past 100 years or so, we have been able to produce preservatives that can substantially lengthen the usability of wood and reduce rot/decay (for example, treated lumber). Wood can also shrink and warp, problems that have been reduced or nearly eliminated by new sawing methods and by air-drying and/or kiln-drying lumber and timbers.
Within the relatively recent past, we have improved our ability to obtain longer pieces of wood that have sufficient strength and meet building codes, allowing for taller and larger buildings to be built. Over the past 40 or 50 years, we have greatly enhanced techniques to produce extended lengths and widths of wood that possess structural characteristics similar to the more conventional steel and concrete products such as greater spans, load-bearing capacity, precision, and predictability. These improvements allow us the ability to build taller, larger, and more complex wood products, often referred to as “mass timbers.” One type of mass timber that is gaining popularity is cross-laminated timber, commonly referred to as CLT.
CLT is made of various pieces of lumber glued together using wood adhesives to produce a layer (a shortened example is shown in Figure 1). These layers of glued pieces of lumber are then placed on top of one another in alternating right-angle (90-degree) directions. The final form of CLT timber is held together by further wood adhesive (Figures 1 and 2). This mass timber is simply another form of long-used engineered wood, such as glulams and plywood, which have been around for many years.
Laying several pieces in 90-degree alternating directions distributes the load-bearing capacity across different planes of the wood product. Therefore, we can more fully utilize the load-bearing properties of wood’s radial, tangential, and longitudinal characteristics. This allows CLT to be used to span two directions, allowing for point-loaded support without the need for beams, for example.
Engineered wood has been defined as building products made by binding wood fiber (in the form of strands or veneers—strands in the case of oriented-strand board [OSB]) with moisture-resistant structural adhesives and orienting the fiber in specific directions to achieve desired levels of strength, stiffness, and stability. Engineered wood products such as plywood, OSB, waferboard, particleboard, and medium-density fiberboard (MDF) are precursors to CLT and other mass timbers such as laminated veneer lumber (LVL) and parallel strand lumber (PSL). For both plywood and OSB, layers of initial product are laid down on top of each other in cross-direction to better utilize the structural properties of wood. In the case of OSB, these are layers of strands/flakes; in the case of plywood, peeled plies of wood.
As with other engineered wood products, CLT products in many ways randomize the natural characteristics of solid wood, such as knots and irregular grain, minimizing their impact on strength. Hence, CLT is a “piece” of wood of increased uniformity and structural performance.
Brief History of CLT
The development of CLT is credited to individuals in Austria and Germany during the early 1990s (FPInnovations 2013). Acceptance of this product was initially slow, but construction using CLT has significantly increased since the early 2000s. CLT was created mainly due to the demand for buildings to be constructed using alternative wood-based products. Despite the long history of wood’s use in construction, our ability to build taller and larger structures using wood has been limited by our inability to produce pieces of sufficient strength, size, and length. Additionally, CLT has become more popular throughout the world, but more specifically in the U.S., because of concerns related to global warming and climate change. It is hoped that CLT can produce buildings, most specifically nonresidential structures, that are structurally sound and safe but can also serve as long-term sources of carbon sequestration and storage, helping to reduce the amount of carbon in the atmosphere. With time, fasteners and connectors have been improved, providing greater confidence in the stability and strength of CLT-constructed buildings.
Cutting boards and tabletops made by joining pieces of wood together are in many ways miniature precursors for CLT and other mass timbers. For centuries, relatively tall nonresidential buildings, such as churches and barns, were built in Europe using solid wood timbers. Other buildings throughout the world, such as cabins and lodges (Yosemite Lodge, for example), were built of solid wood timbers and logs. In the U.S., iron, steel and concrete started to replace wood as framing for buildings around the early 1900s because of the desire to build taller, larger, and more complex buildings, as well as the inability to obtain pieces of wood of sufficient length and size. The Chicago Fire of 1871 also contributed to the reduction of building nonresidential buildings of wood. Much of Chicago was destroyed during this fire, making people more concerned about the integrity of entire wood-based buildings.
In the U.S., most CLT construction has not used southern yellow pine. Other species include Douglas-fir, grand fir, western larch, Sitka spruce, and lodgepole pine, among several other western U.S. conifer species. Due to the high cost of transportation, it is difficult to ship CLT across the country, which has limited the amount of CLT construction in the Southeast. However, there are two new large-scale production facilities in the region: SmartLam in Dothan, Alabama, and Structurlam in Conway, Arkansas. These facilities will substantially increase the feasibility of using southern yellow pine CLT for building projects in the Gulf region. Additionally, a smaller operation called Texas CLT located in Magnolia, Arkansas, produces custom-built CLT pieces.
CLT pieces are currently made of either three, five, seven, or nine layers/plies (Figure 2). They often range in width from 8 to 12 feet (Figure 3) and can be up to 60 feet in length. Currently in the Southeast, CLT is most often constructed using lumber grade 2 southern yellow pine of dimensions of 2x10, 2x8, 2x6, or 2x4. To enhance appearance, some CLT is constructed where the exterior layers use Prime grades of lumber.
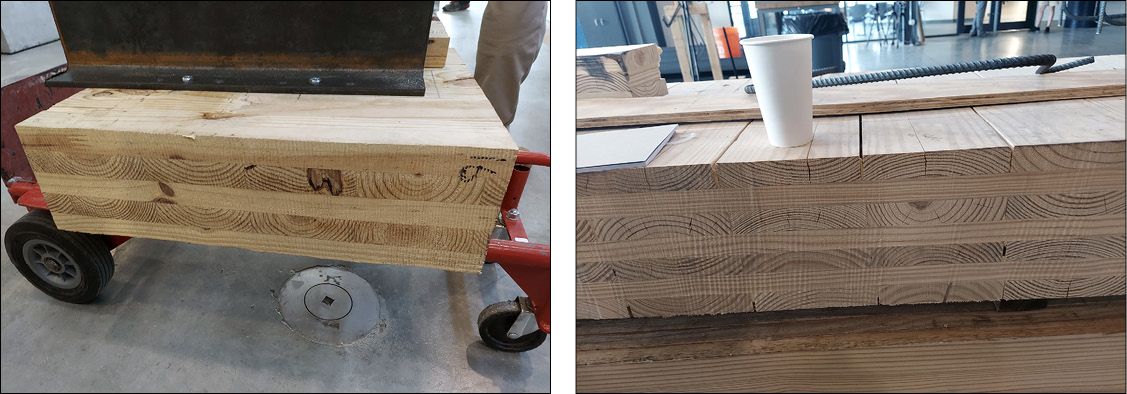
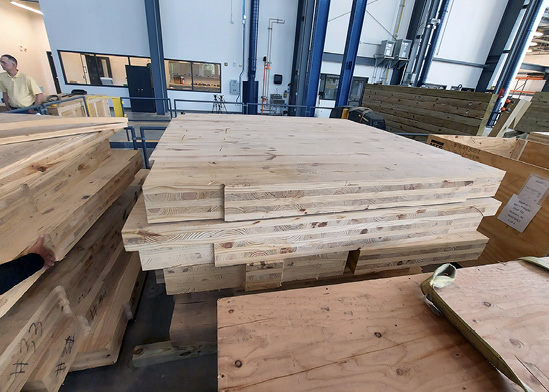
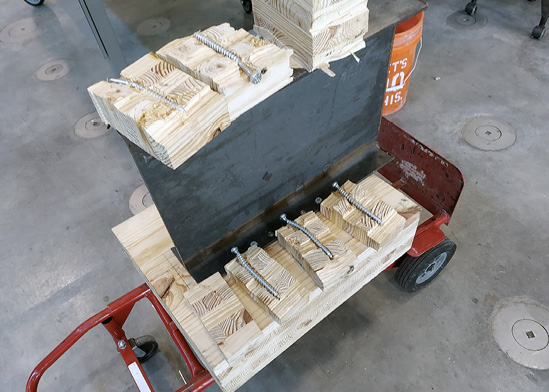
Advantages of CLT Construction
There are several possible advantages of using CLT during construction of nonresidential buildings. One advantage is that CLT and other mass timbers are often more visually appealing than steel and concrete, and people often prefer to live and work in wood structures. Wood’s color, texture, fresh pine scent, visually appealing grain, and warmth to touch are desirable characteristics. Additionally, CLT is lighter than steel and concrete, reducing loads and foundation sizes.
When using the material, construction is often quieter and safer and has less impact on the site itself. Exact piece sizes and shapes required by a job site can be prefabricated within a processing facility. Therefore, the on-site construction of the building itself is often faster than the more conventional steel and concrete. Since CLT is prefabricated, there is often far less onsite waste. Plus, labor costs are often lower because smaller work crews are needed and the length of construction time is shorter relative to conventional construction. CLT is a long-term source of carbon sequestration and storage.
Building with CLT requires less carbon overall to construct a building, which is one component of what is often referred to as the amount of “embodied carbon” in the mass-timber industry. Embodied carbon refers to the so-called “carbon footprint” of a building—the greenhouse-gas emissions that result from manufacturing, transporting, installing, maintaining, and disposing of building materials. Further, many people feel that these buildings have superior thermal properties and moisture control, which result in less heat loss and greater comfort for occupants. CLT could be advantageous in areas with both very cold and hot weather to help mediate a constant building temperature. Carbon emissions that come from energy, heat, lighting, and other factors are commonly referred to as “operational carbon” in the mass-timber industry. Wood buildings are also often better able to absorb sound.
Research is being conducted on whether bug-killed and blue-stained wood (resulting from not harvesting/utilizing the wood immediately after death/felling, perhaps due to hurricanes or tornadoes) can be used in constructing mass timber and CLT buildings. This ability would be highly beneficial for the utilization of these types of logs.
Disadvantages of CLT construction
Currently, CLT (and mass timber in general) is more expensive than the more conventional steel and concrete construction materials. However, in some cases, the total building cost of mass-timber construction is less expensive. Remember, some of the advantages of CLT and mass-timber construction are the prefabrication of the pieces, smaller work crews, and lighter weight that can require smaller foundations, all of which reduce costs for some projects.
Another issue is that there is a limited number of work crews familiar with mass-timber construction in general but CLT in particular. Currently, the supply of CLT material can be problematic, and there are only two large-scale processing facilities in the Southeast. These issues create problems with product availability and transportation costs. However, if CLT becomes more popular over time, the number of facilities will likely increase. Several other companies have already announced their intention to produce CLT using southern yellow pine lumber. Variations in the grade of lumber and CLT can also result in varying prices.
Currently, there can also be issues with onsite storage of CLT at building sites because of rain and potential damage (decay) to the product itself, both short term and long term. Depending on the building code used in a given state or area, there are often issues with code restrictions regarding building heights; if extremely tall buildings are desired, construction with CLT and mass timber will need to use an “alternative means” procedure in building code official approval. Also, since CLT is still relatively new, there is less familiarity with its performance and thus less confidence in CLT construction. Further, there can be some problems with using concealed spaces to “hide” electrical, plumbing, and other services. Hence, many mass timber buildings have exposed systems.
CLT-Constructed Buildings
According to WoodWorks.org, as of March 2022, 1,384 “mass timber projects” had been constructed or were in design across the 50 states within the multifamily, commercial, or institutional categories. Throughout the United States, it is reported that 305 buildings using some amount of CLT have either been built or are starting construction. Further, 426 buildings using some amount of CLT are in design. CLT can not only be used for roofs and ceilings, but also the construction of entire structures. Currently, there are mass-timber-built buildings as tall as 25 stories in the U.S.
Further Reading
FPInnovations. 2013. CLT handbook: cross-laminated timber. Edited by E. Karacabeyli and B. Douglas. Pointe-Claire, Quebec. 572 p.
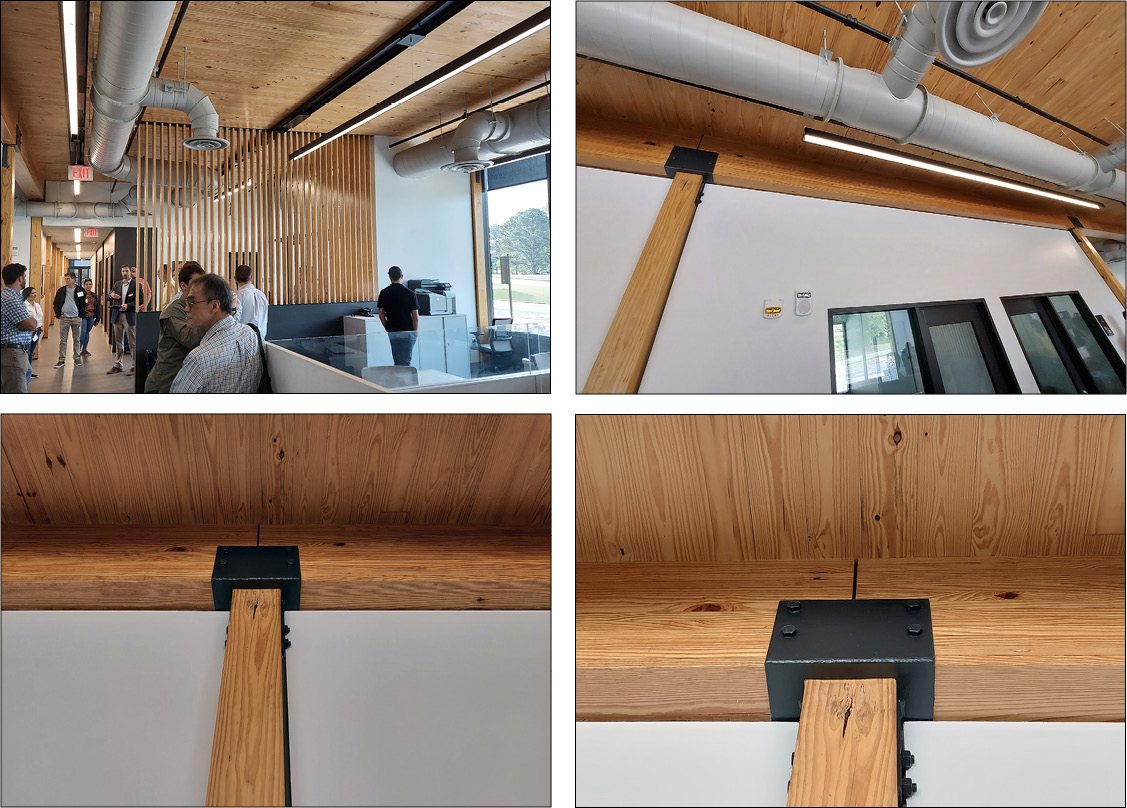
The information given here is for educational purposes only. References to commercial products, trade names, or suppliers are made with the understanding that no endorsement is implied and that no discrimination against other products or suppliers is intended.
Publication 3855 (POD-1-23)
By Curtis L. VanderSchaaf, PhD, Assistant Professor and Extension Specialist, Central Mississippi Research and Extension Center, Mississippi State University; Laya Khademibami, PhD, Assistant Research Professor, MSU Department of Sustainable Bioproducts; and Adam Maggard, PhD, Harry E. Murphy Associate Professor and Extension Specialist, College of Forestry, Wildlife, and Environment, Alabama Cooperative Extension System, Auburn University. We would like to acknowledge Auburn University for hosting the conference “The Sustainable Future of CLT in the South: Grow. Design. Build.” We would also like to thank the MSU Department of Sustainable Bioproducts. Pictures presented in Extension Publication 3855 were taken at the conference. In addition, we want thank Tom S. Chung, Principal, Leers Weinzapfel Associates, and Pat Layton, PhD, Director, Wood Utilization + Design Institute, Clemson University, for very useful comments.
The Mississippi State University Extension Service is working to ensure all web content is accessible to all users. If you need assistance accessing any of our content, please email the webteam or call 662-325-2262.